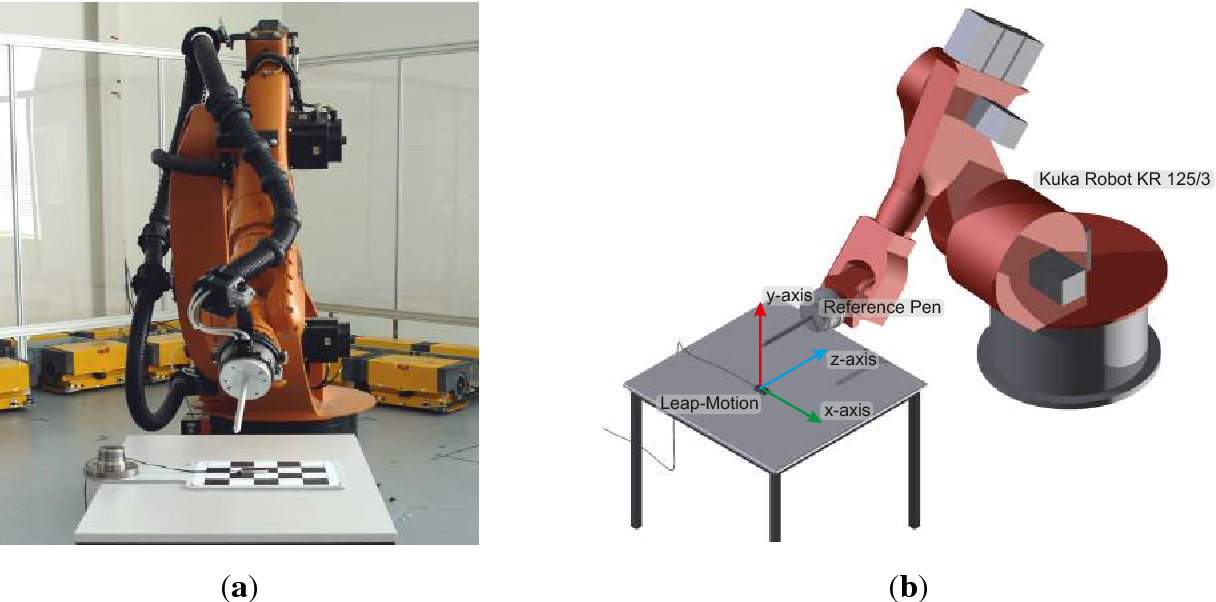
Figure 2 from Analysis of the Accuracy and Robustness of the Leap Motion Controller | Semantic Scholar
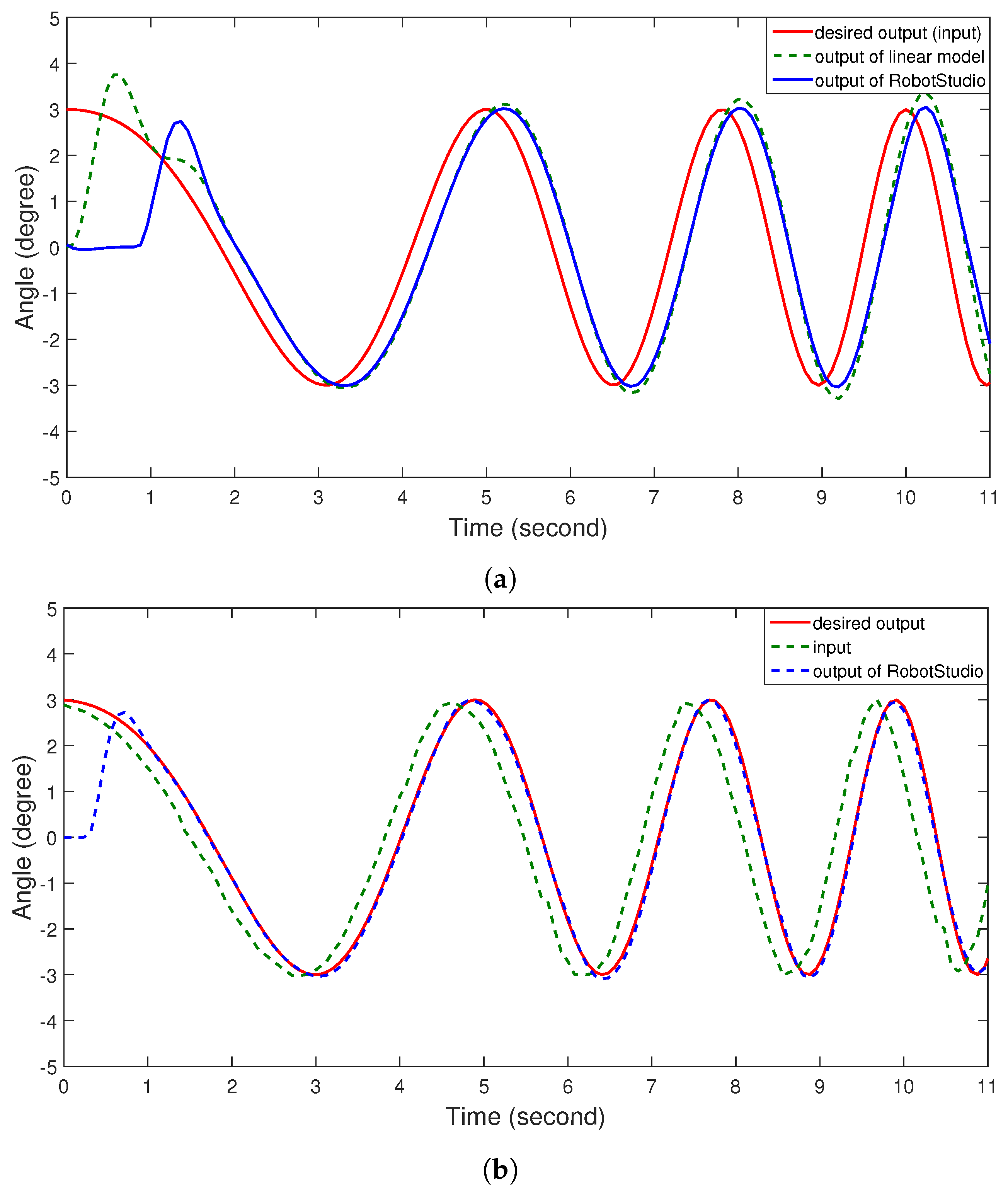
Robotics | Free Full-Text | Industrial Robot Trajectory Tracking Control Using Multi-Layer Neural Networks Trained by Iterative Learning Control | HTML
Improving Robotic Machining Accuracy through Experimental Error Investigation and Modular Compensation
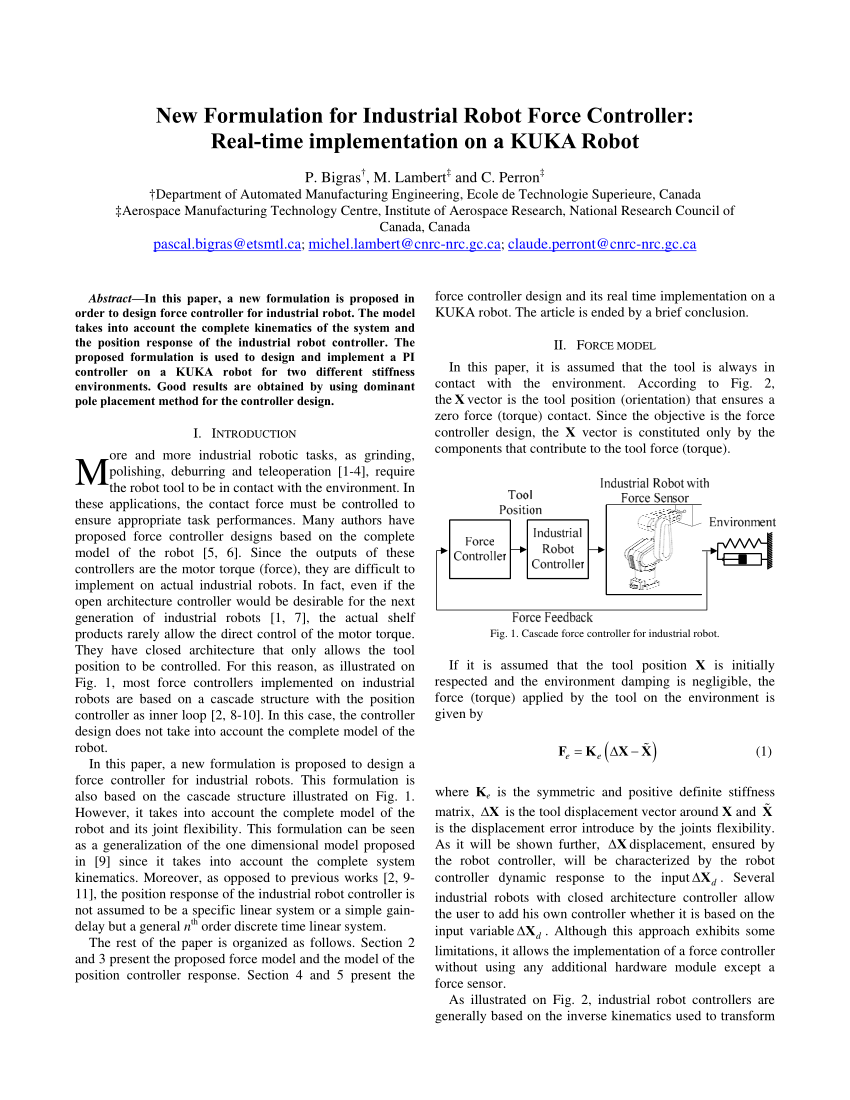
PDF) New formulation for an industrial robot force controller: Real-time implementation on a KUKA robot
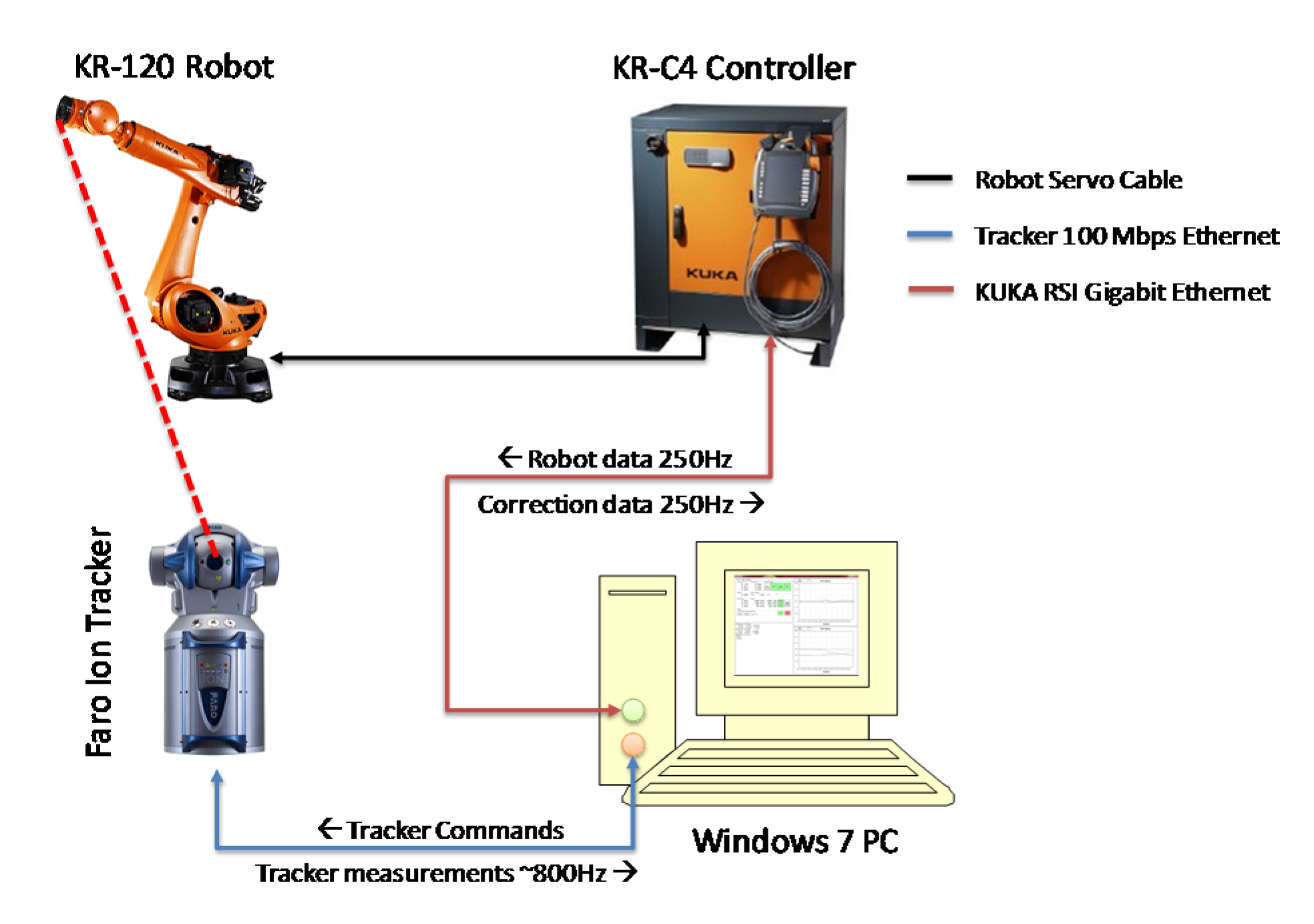
JMMP | Free Full-Text | Real-Time Laser Tracker Compensation of Robotic Drilling and Machining | HTML
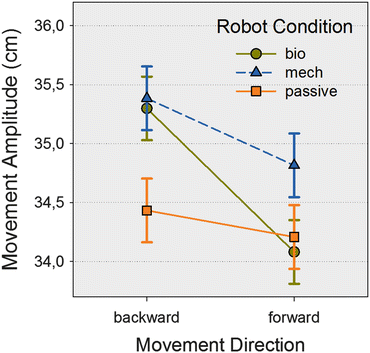
Man-Robot Collaboration in the Context of Industry 4.0: Approach-Avoidance Tendencies as an Indicator for the Affective Quality of Interaction? | SpringerLink

Robotic path planning for non-destructive testing – A custom MATLAB toolbox approach - ScienceDirect

PDF) Singularity Avoidance by Virtual Redundant Axis and its Application to Large Base Motion Compensation of Serial Robots
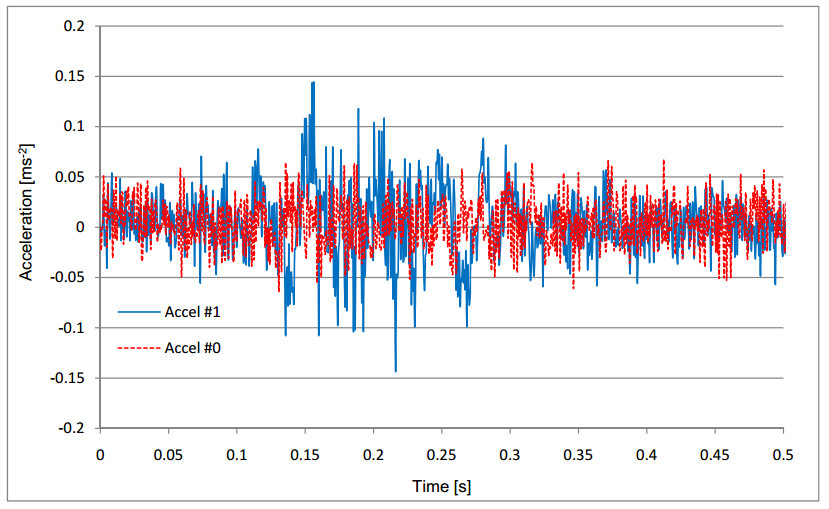
Motion optimisation for improved cycle time and reduced vibration in robotic assembly of electronic components
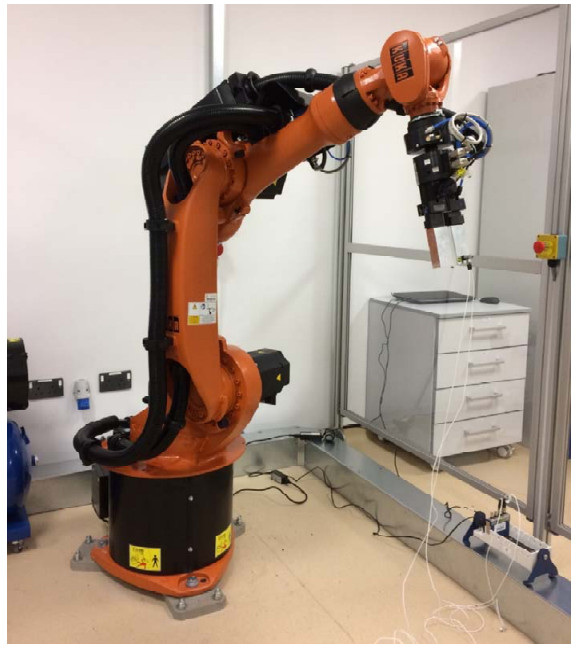
Motion optimisation for improved cycle time and reduced vibration in robotic assembly of electronic components
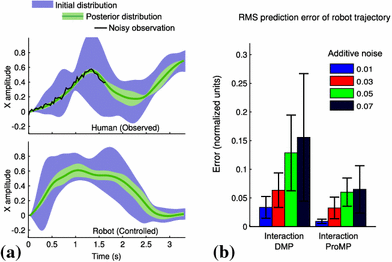
Probabilistic movement primitives for coordination of multiple human–robot collaborative tasks | SpringerLink
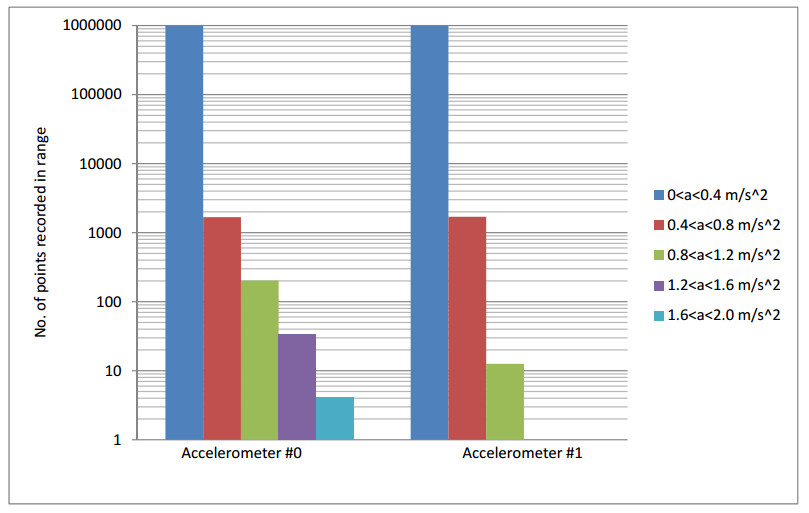